Many companies are managing their BOMs in ERP rather than a PLM system due to the desire for better data reporting in the ERP. Although this is understandable, there are plenty of use cases for managing a BOM in a PLM system such as Windchill. Many businesses utilizing Windchill are not taking advantage of its full range of features. Let’s explore Windchill’s BOM management capabilities as well as the benefits of managing BOMs in PLM systems.
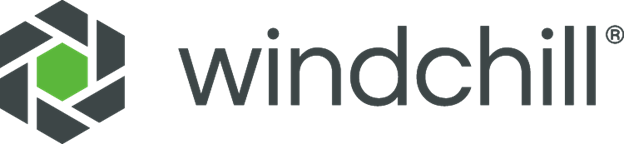
Utilizing PLM Systems for BOM Management
Even with a PLM, it is common for manufacturers to have multiple disconnected systems that need help keeping up with their business processes. Additionally, they frequently lack a much-needed part-centric BOM. When stakeholders are forced to work outside of their PLM system, data management becomes fragmented and ineffective. Trying to share BOMs across teams risks errors and often causes downstream teams to work with out-of-date information. Properly utilizing the right PLM system and BOM strategy can help organizations configure and manage product information during every step of the product lifecycle.
Part-Centric BOMs
A proper BOM acts as one source of truth to depend on, creating a complete digital product definition within your PLM system. A digital product definition configures, manages, and stores all product-related content in a single, central repository. This reduces data and system complexity, resulting in a more efficient workflow. The digital product definition then connects to major systems by weaving through downstream data sets, creating the digital thread. Part-centric BOMs help ensure products are configured accurately, resulting in less rework, less waste, and faster time to market. The part design allows every department to agree on what the customer receives from the product. Manufacturing engineers may then create a manufacturing BOM (or mBOM) if desired.
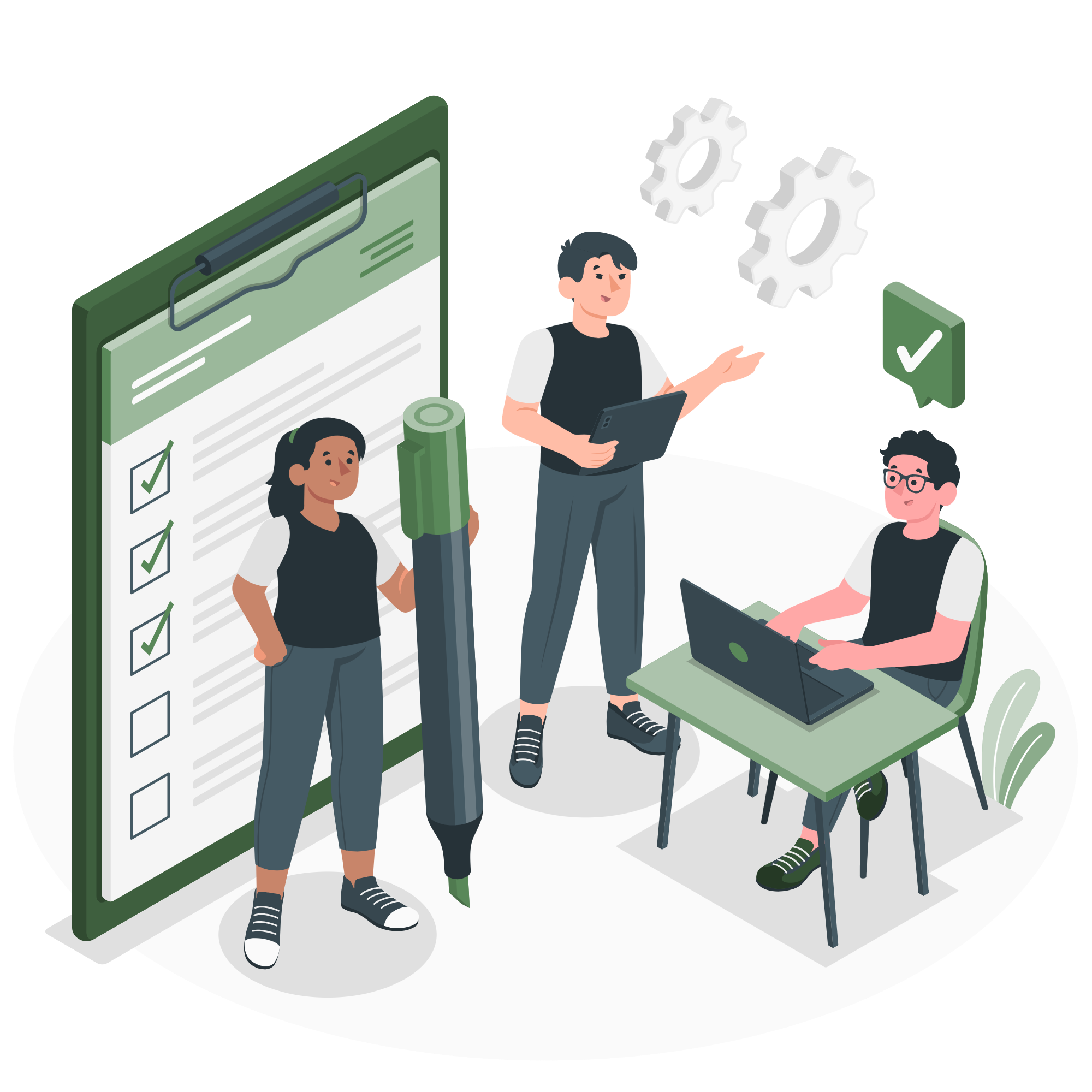
Benefits of BOM Management in a PLM System
Managing BOMs within a PLM system has more benefits than you may think. Let’s explore all the strengths PLM systems provide.
Visibility
Integrating a BOM with PLM may provide early visibility to stakeholders. PLM systems provide early, continuous access to a single source of product information. This enables better collaboration between cross-functional engineers in early development phases. The early phases of a new product introduction (NPI) are often complicated and difficult to view for certain teams. If for example a member of a team other than the product developers want to view information early in the development process, it can be ambiguous and confusing. PLM software allows developers to share pieces of information based on the role of the team member receiving it. This reduces confusion by allowing the team member to receive only the necessary information. Overall the visibility PLM systems provide allows team members to complete their tasks on time and provide feedback with a better understanding of the product.
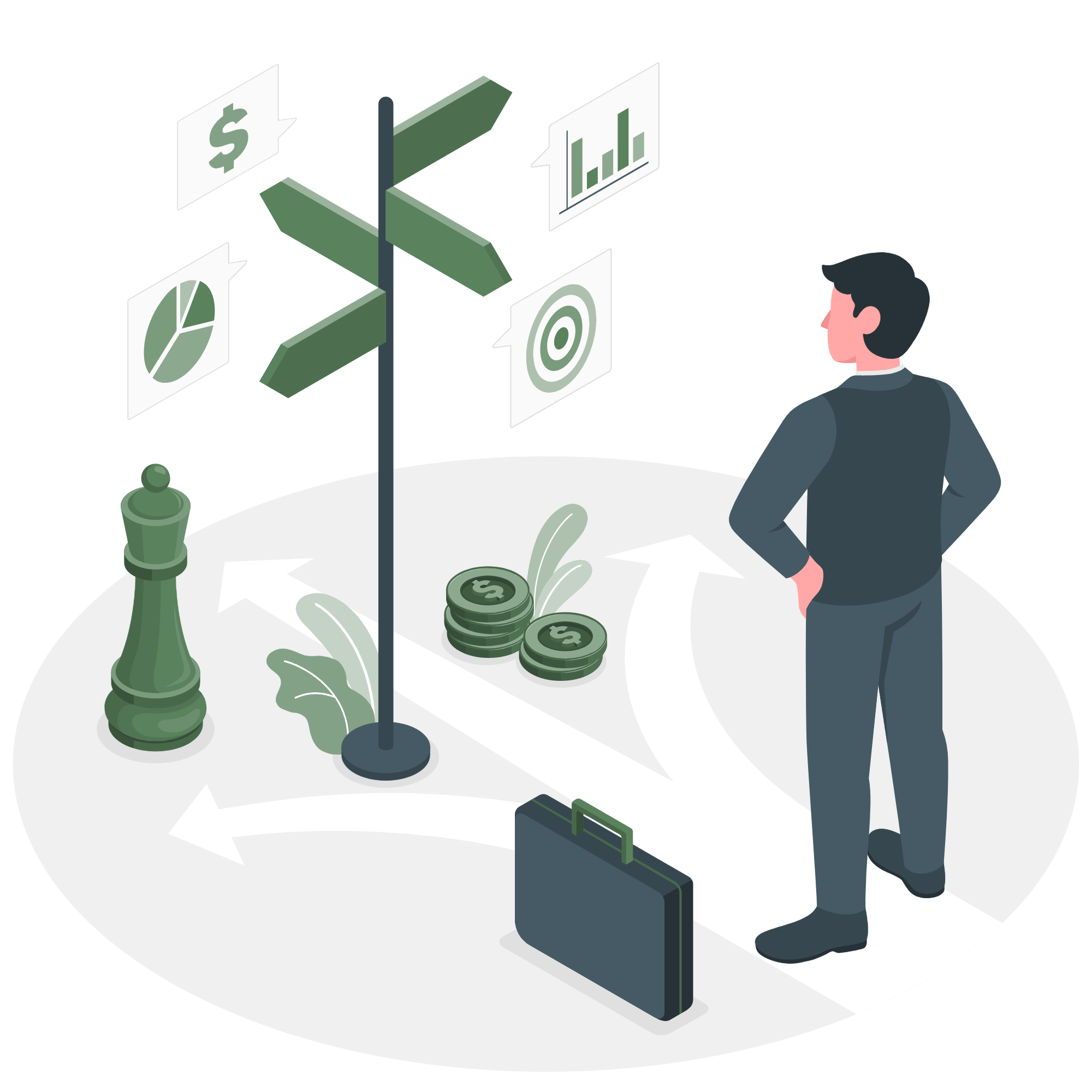
Range of BOM Structures
PLM systems often support a wider range of BOM structures compared to ERP systems. This is because PLM systems are designed to manage the entire lifecycle of a product, from initial design through end-of-life while ERP systems focus more on planning and sales. Organizations can structure a BOM based on the types of products they sell and the strategies they use to bring their products to market. Additionally, BOMs can take multiple forms, such as a static BOM for a one-off product, or a BOM that can be configured to satisfy a whole market. PLM systems offer specific BOM views for departments that ensure traceability between parts. This allows every team to gain a deeper understanding of the digital product definition.
Configuration Management
With products constantly being altered, it’s important to track these changes in real time. Disconnected systems make it difficult to accurately capture all of the alterations, but a PLM system enables everyone to receive accurate, up-to-date information. Managing these configurations is more than just BOM management, it includes any relationship within the PLM system. For example, how historical content relates to a product. These connections make traceability critical, as accessing the current version of related information is just as important as BOM access. PLM systems have a digital thread with BOM at the foundation, often creating a closed-loop system. These systems automatically incorporate the configuration flow from upstream definitions into downstream configured BOMs.
Visualization
Digital models are powerful but require advanced configuration management, similar to BOMs. This is because poorly managed visualizations can rapidly spread incorrect information. When utilized correctly, visualization helps with part recognition and can optimize downstream processes and deliverables. Oftentimes, PLM and ERP systems will utilize a snapshot approach which involves capturing and storing the state of product-related data at a specific point in time. However, any PLM system using a snapshot approach requires a trigger when changes take place to ensure out-of-date visuals do not get shared. While ERP systems will often pass snapshots at release, PLM systems require that the data has been reviewed and locked to ensure its accuracy.
Part Reuse
PLM supports two approaches to help solve the challenge of part reuse in the enterprise. The first approach is classification. Classification makes parts easy to break down by category by adding information to the part’s description. Category examples include hardware, electrical, sourced components, etc. Another way to better manage product reuse is through supplier management. Parts are frequently sourced from external suppliers and to optimize product reuse, the enterprise needs to understand which parts can be sourced from which suppliers. PLM systems make it possible to list and track each vendor and the parts they offer. Furthermore, a BOM can show the relationship between the part and the supplier. The combination of classification and supplier management helps improve part reuse and provides the enterprise with better information about the parts, enabling users to quickly find the parts they need.
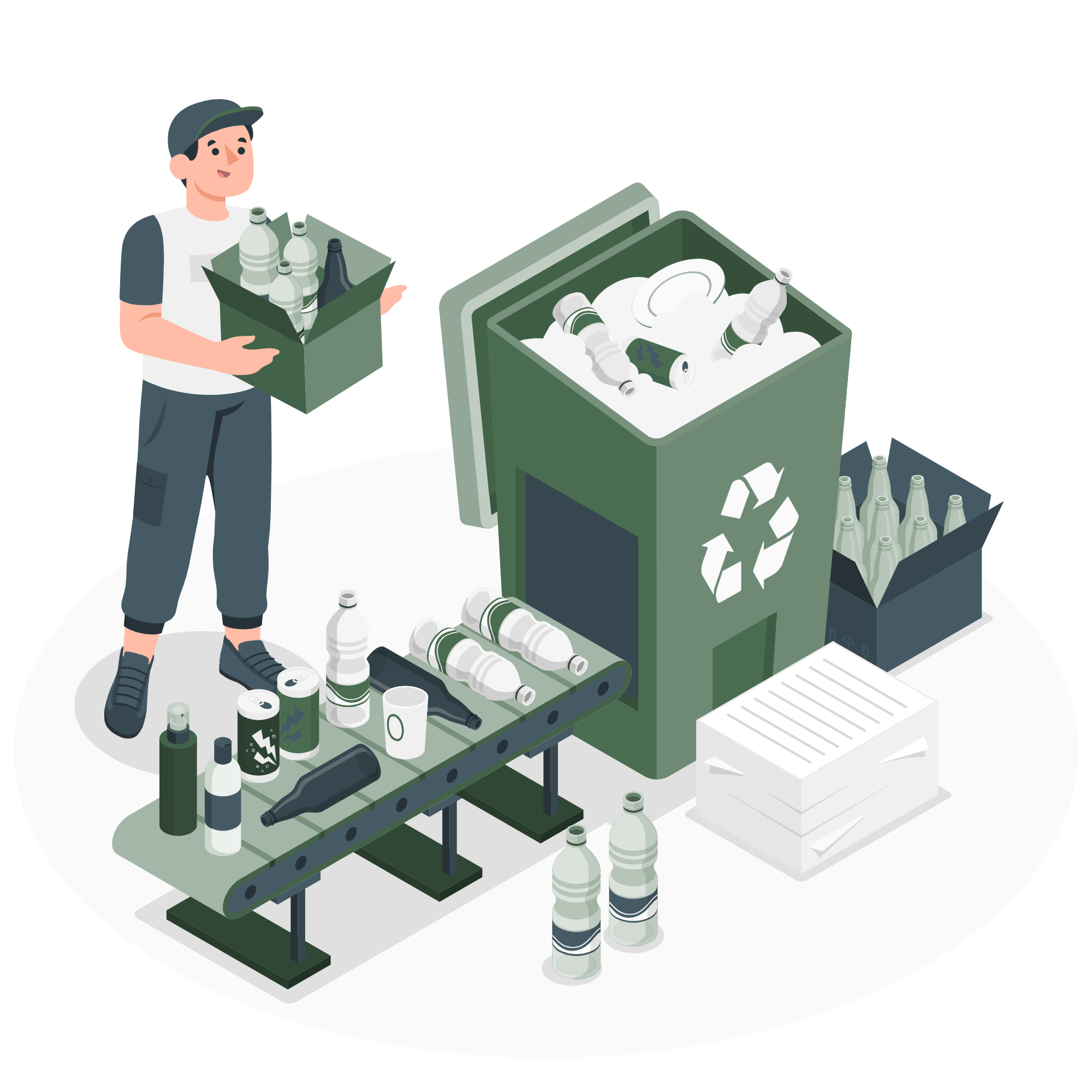
Optimize Downstream Utilization
PLM systems can optimize workflows by ensuring data accuracy and the configuration of upstream and downstream deliverables. Downstream functions, for example, can use data from the engineering BOM to create their own respective deliverables in parallel. These functions include supply management, manufacturing planning, and services. Additionally, cross-departmental collaboration and process acceleration require early visibility of actionable information. Accurate and complete visualization enables downstream teams, such as manufacturing, to create deliverables such as work instructions to develop technical service procedures. These functions allow organizations to reduce rework, speed up product development release cycles, and decrease time to market.
IP Protection
IP protection is vital for companies wanting to optimize collaboration without risking IP loss or failing to meet regulatory requirements. PLM systems manage all information throughout the product lifecycle so integrating IP protection ensures that valuable intellectual property is safeguarded against unauthorized access, use, and theft. While enforcing IP policy synchronization across multiple systems can be complicated and time-consuming, utilization of a PLM solution that can effectively manage all elements of collaboration allows organizations to avoid IP loss.
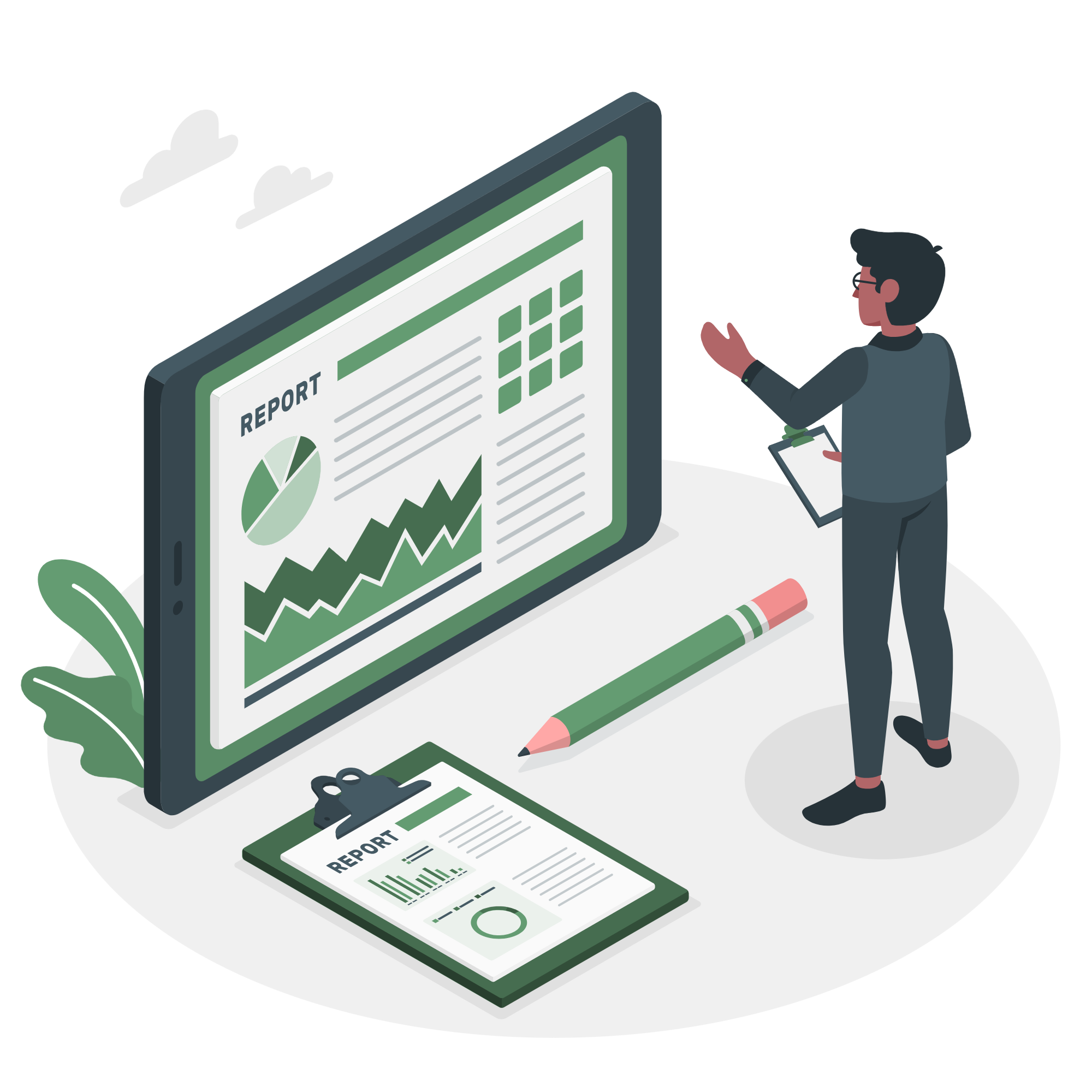
BOM-Based Reports
A key benefit of a PLM system is its ability to provide a wide range of reports for an organization. These reports encourage inquiries and product analyses, enabling users to better understand the digital product definition. Additionally, PLM systems satisfy demands for more interactive ways to understand and work with data. Users are provided with easier ways to receive information, which facilitates more informed decisions in the development process.
BOM Transformation
While many enterprises rely on just one view of the BOM, there is a way to transform it to appeal to each team. Most BOM structures are designed to suit the engineering team, but PLM allows BOM transformation. BOM transformation allows a group to manipulate the original BOM to a view that works for them. For example, the manufacturing group could manipulate the engineering view for production planning. There are a few key benefits of this feature. First, it allows teams to plan their BOMs earlier in the process rather than wait for engineering to finish their drawings. Next, BOM transformation enables manufacturing to deliver not just one plan, but multiple plans specific to different production plants. Additionally, comprehensive digital product definitions enable users to easily transform BOM structures and keep them organized. This allows manufacturing engineers and service planners to better understand their tasks. A robust digital product definition can also make it easy for users to see and track any discrepancies as they perform their BOM transformation.
Ready to Implement PLM for BOM Management?
While it may be challenging to implement every single PLM best practice we covered, with each win, your organization will see tangible, positive business outcomes. Utilizing a PLM system for BOM management allows product data to be managed and implemented to its full potential. If you have questions about this implementation or want to get started with Windchill today, contact our experts.