When working in the engineering and manufacturing fields, it is common to encounter unfamiliar terms. In this glossary, we define important terms that describe processes and components in the engineering, manufacturing, service, and sustainability industries.
General Terminology
Attrition/ Turnover Costs
Employee turnover or attrition cost is the cost to hire a replacement employee and train that replacement. The training costs should include all costs to get the new employee to the same level of productivity as the employee who left.
Capital Investment
A capital investment is a sum of money that goes towards furthering the objectives of a business. Oftentimes this includes purchasing long-term assets for the business. There are technically two different ways this term is used in a business context. The first refers to funds put toward helping the business achieve its goals. The second refers to funds used to purchase fixed assets for the business, not for daily operations. In either case, a capital investment typically involves a lump sum that is to be used with the growth of the company in mind.
Compliance Costs
Compliance costs refer to all business expenses caused by adherence to industry regulations. This can include payroll for the compliance department, regulatory reporting costs, and any systems required for the process. Compliance costs for a company increase with the industry regulation standards. Companies that do not comply with regulations can incur heavy fines from the regulatory body.
Enterprise Resource Planning (ERP)
Enterprise Resource Planning (ERP) is the preparation of acquired business resources (materials, employees, customers, etc.) to be moved from one state to another. An ERP system is a business support system that maintains the data needed for business functions such as Manufacturing, Supply Chain Management, Financials, Projects, Human Resources, and Customer Relationship Management.
ISO Compliance
ISO compliance is adhering to the requirements of ISO standards without the formalized certification and recertification process. For example, organizations may choose to follow guidelines for establishing a quality management system as outlined in ISO 9001.
Key Performance Indicator (KPI)
KPIs are quantifiable measures used to evaluate the success of an organization, employee, etc. in meeting objectives for performance.
Net Promoter Score (NPS)
Net Promoter Score (NPS) is a management tool that gauges the loyalty of a firm’s customer relationships. The Net Promoter Score is calculated based on responses to a single question: How likely is it that you would recommend our company/product/service to a friend or colleague? The score is most often ranked on a 0 to 10 scale.
New Product Introduction
New Product Introduction (NPI) is the process that takes an idea from an initial working prototype to a thoroughly refined and reproducible final product. Since NPI requires a substantial investment of time and resources, careful planning goes into each step to ensure that the result will be worth the effort. Businesses must consider product development costs, time-to-market, manufacturing efficiency, and product quality to succeed in their NPI.
Product Quality
Product quality is based on the ability to incorporate features that meet consumer needs. Companies achieve customer satisfaction by producing high-quality products, free from any deficiencies or defects.
Standard Operating Procedure (SOP)
A standard operating procedure is a set of step-by-step instructions compiled by an organization to help workers carry out routine operations. SOPs aim to achieve efficiency, quality output, and uniformity of performance while reducing miscommunication and failure to comply with industry regulations.
Time to Productivity
Time to productivity is a metric measuring how long it takes a new hire to contribute to an organization. The effectiveness of the onboarding program, the experience of the candidate, and job support generally influence this metric. All three of these work together to optimize the time to productivity.
Training Time
Training time is the time it takes to train new workers & existing technicians on new procedures or working methods. Training can be an expensive & time-consuming activity so the goal is to achieve the most efficient way to train employees.
The costs involved in training can be broken down as follows:
- Direct cost: Compensation cost of the trainee (trainees are still being paid while they’re in training).
- Opportunity cost: Lost productivity of the trainee.
- Operational cost: Cost of training equipment, training facility, trainee travel & living expenses, 3rd party training costs.
Software/Hardware Terms
Agile Software Development
Sometimes referred to as just “Agile”, Agile Software Development is a development approach that involves flexible planning and continuous improvement to deliver the software as fast as possible. This overall methodology has specific approaches such as Scrum, Kanban and others.
Continuous Integration (CI)
Code Refactoring
Code Refactoring is the process of editing code to reduce or eliminate technical debt.
DevOps
DevOps, which is a combination of Development and IT Operations, is the concept of software developers producing smaller batches of software work, deployed more frequently, with less planning and more adaptability by people working better together.
Dynamic Data Exchange (DDE)
Dynamic Data Exchange (DDE) is a form of Inter-Process Communication (IPC) in the Microsoft Windows operating environment. When two or more applications that support DDE are running simultaneously, they can exchange information, data, and commands. DDE has been enhanced with Object Linking and Embedding (OLE) technology.
Git
Graphical User Interface (GUI)
Graphical User Interface (GUI) enables a user to interact with a software application through graphics instead of text.
Hypertext Transfer Protocol (HTTP)
Hypertext Transfer Protocol (HTTP) is a connectionless client/server protocol used ubiquitously in IT and the web. Hypertext is the structured text that uses logical links (hyperlinks) between nodes containing text. For example, a web browser may be the client and an application running on a computer hosting a website may be the server. HTTP resources are identified and located on the network by unique Uniform Resource Locators (URLs).
Internet of Things (IoT)
The Internet of Things (IoT) is the network of physical objects or “things” containing embedded electronics, software, sensors, and network connectivity that enables these objects to collect and exchange data. These “things” are commonly appliances, lightbulbs, or switches. The Industrial Internet of Things (IIoT) is about connecting industrial operations. For example, connecting dissimilar networks, devices, protocols, and applications in a manufacturing plant. It shares and connects this data and then turns it into actionable information used to make specific business decisions.
Information Technology (IT)
Information Technology (IT) is a broad term used to describe the application of computers and telecommunications equipment to store, retrieve, transmit, and manipulate data. Oftentimes this is in the context of a business or other enterprise. In industrial automation, IT often plays an important role in OT, however, OT often has unique technology separate from IT.
Kanban
Kanban is an Agile project management methodology for lean manufacturing. Taiichi Ohno, an industrial engineer at Toyota, developed kanban to improve manufacturing efficiency. The system takes its name from the cards that track production within a factory. Kanban is also known as the Toyota nameplate system in the automotive industry, but has most recently been used as a software development methodology that visualizes work, and limits work-in-progress to focus on achieving completed work, among other things.
Operations Technology (OT)
Operations Technology (OT) is hardware and software that detects or causes a change through the direct monitoring or control of physical devices, processes, and events in the enterprise. OT technology works together to achieve an industrial objective such as manufacturing, transportation of matter, or generation of energy. OT technology may be dependent on IT technology for communication at the business or enterprise level.
Open Database Connectivity (ODBC)
Open Database Connectivity (ODBC) is a standard programming language middleware API for accessing database management systems (DBMS). The designers of ODBC aimed to make it independent of database systems and operating systems. An application written using ODBC can be transported to other platforms, both on the client and server side, with few changes to the data access code. Open Database Connectivity (ODBC) is a Microsoft standard for accessing different database systems from Windows such as SQL, Access, or Oracle.
Open Platform Communications (OPC)
Open Platform Communications (OPC) is a set of standard interfaces based on Microsoft’s OLE/COM technology. The OPC standard interface makes interoperability between automation/control applications, field systems/devices, and so on possible.
OPC Client
An OPC Client is a software application that connects to an OPC Server to receive data from a process. OPC Clients are based on a Client/Server Architecture.
OPC Data Access (OPC DA)
OPC Data Access (OPC DA) provides access to real-time process data. Using OPC DA, one can ask the OPC server for the most recent value of flows, pressures, levels, temperatures, densities, and more. For historical data see OPC Historical Data Access (OPC HDA).
OPC Historical Data Access (OPC HDA)
OPC Historical Data Access (OPC HDA) is used to retrieve and analyze historical process data. This data is typically stored in a Process Data Archiver, a database, or an OPC HDA server. An OPC Server is a software application that acts as an API (Application Programming Interface) or protocol converter. An OPC Server will connect to a device such as a PLC, DCS, RTU, or a data source such as a database. This device data is translated into a standards-based OPC format. OPC-compliant applications such as an HMI, SCADA, historian, spreadsheet, or trending application may connect to the OPC Server and use it to read and write device data. OPC Servers are based on a Server/Client architecture.
OPC Unified Architecture (OPC UA)
OPC Unified Architecture (OPC UA) is an updated standard to modernize and enhance all the functionality of the existing OPC-defined interfaces. It is a platform-independent, service-oriented architecture that integrates all the functionality of the individual OPC Classic specifications into one extensible framework. OPC UA is described in a layered set of specifications broken into parts. This layering helps isolate changes in OPC UA from changes in the technology used to implement it.
Operating System (OS)
Operating System (OS) is a software program that manages the basic operations of a computer system. These operations include memory appointment, the method of handling tasks, the flow of information into and out of the main processor and to peripherals, etc.
Representational State Transfer (REST)
Representational State Transfer (REST) is a stateless model where clients can access resources on a server via requests. In most cases, a resource is a device and the data that a device contains. REST systems typically communicate over Hypertext Transfer Protocol (HTTP) with the same HTTP verbs that web browsers use to retrieve web pages and send data to remote servers. These verbs include but are not limited to GET, POST, PUT, and DELETE.
Remote Terminal Unit (RTU)
A Remote Terminal Unit (RTU) is an industrial data collection device that communicates data to a host system by using telemetry (such as radio, dial-up telephone, or leased lines). As its name suggests, these units are typically located at a remote location.
Scaled Agile Framework (SAFe)
The Scaled Agile Framework is a set of organization and workflow patterns intended to guide enterprises in scaling lean and agile practices. SAFe is one of a growing number of frameworks that seek to address the problems encountered when scaling beyond a single team
Scrum
Scrum is a project management methodology for effective team collaboration based on Agile software development.
Simple Network Management Protocol (SNMP)
Simple Network Management Protocol (SNMP) is used in network management systems to monitor network-attached devices for conditions that warrant administrative attention. It consists of a set of standards for network management, including an Application Layer protocol, a database schema, and a set of data objects.
Software Development Life Cycle (SDLC)
The general process of software development that follows a series of steps until the end of life of the software.
Transmission Control Protocol over Internet Protocol (TCP/IP)
Transmission Control Protocol over Internet Protocol (TCP/IP) refers to a common data transport protocol stack in which data is placed within TCP frames and transmitted across a network using the Internet Protocol. It is considered a foundational protocol of the modern Internet due to its ability to guarantee message delivery and route across network boundaries.
User Datagram Protocol (UDP)
User Datagram Protocol (UDP) is a connectionless data transfer protocol used with the Internet Protocol (IP).
User Acceptance Testing (UAT)
UAT is a phase of software development where the intended users or business representatives test the software’s features and functionality in a real-world setting to check for compatibility. UAT is also sometimes called beta testing or end-user testing.
Yet Another Markup Language (YAML)
YAML is a human-readable data format for storing and transmitting information and it is commonly used for cloud infrastructure.
Engineering Terminology
Accelerate Product Innovation
Accelerating product innovation means quickly delivering compelling, differentiated products that meet or anticipate customer demands.
Additive Manufacturing
Additive manufacturing (AM) is the industrial production name for 3D printing. It is a computer-controlled process that creates three-dimensional objects by depositing materials, usually in layers. Initially, AM reproduced parts originally designed for traditional manufacturing processes. However, without the limitations of traditional manufacturing processes, products could be designed for additive manufacturing (DfAM), with innovative shapes that couldn’t be previously manufactured with castings or machining. Today, these technologies are often embedded in conventional manufacturing.
Bill of Materials (BOM)
A BOM is a table containing a list of the components required to produce an assembly. A costed BOM includes pricing information while an indented BOM indicates how different components and sub-assemblies relate to one another.
Component
A component is simply, a part. A single, discrete element within an assembly.
Concept Design
Concept design is early-stage design. Not all aspects are resolved, however overall intent or direction is apparent.
Contract Manufacturer (CM)
A CM is an external company that produces parts or products to order.
Cost of Goods Sold (COGS)
Cost of Goods Sold (COGS) measures the “direct cost” incurred in the production of any goods or services. It includes the cost of products or raw materials, (including freight or shipping charges), the direct labor costs of workers who produce the products, the cost of storing products the business sells, and factory overhead expenses.
Cost of Poor Quality (COPQ)
The cost of poor quality comprises costs incurred due to bad practices, failures, and low product quality. This includes:
- Internal failure costs related to the low quality of a product detected before it was shipped. For example, unforeseen waste and scrap or machinery breakdowns attributable to substandard maintenance.
- External failure costs, which are costs related to the low quality of a product detected by the customer after it was shipped. These include returns, complaints, product recalls, service and repairs, warranty claims, and shipping damages.
Cost of Quality
The Cost of Quality (CoQ, also referred to as quality costs) is a method used to measure:
- Cost of Good Quality i.e. the amount of resources used to maintain the quality of products,
- Cost of Poor Quality i.e. the amount of costs incurred due to failures, both internal and external.
Design Reuse Rate
Design reuse allows designers and engineers to leverage information from existing designs in new product development. This allows them to create better products while maximizing value with minimal resources, cost, and effort. The main benefits are:
- An increase in design rapidity and continuity, which has a direct impact on time-to-market.
- Improvements in product quality and reduced errors by using designs you’ve already tested.
- Lowered costs by reducing the number of simulations and tests required to validate a new design or component.
Design Variants
Variant design refers to the technique of adapting existing design specifications to satisfy new design goals and constraints.
Engineering/Enterprise Change Order (ECO)
An engineering change order or enterprise change order, often called an ECO, is used to track product changes and implement these shifts in design. Examples of ECO triggers are the need for product cost reduction, improved product performance, and improved product safety. Extended ECO cycle times can result in delayed product launches, inefficient use of resources & increased costs.
Exploded View
An exploded view is a visual representation of an assembly, showing some or all of the separate components to illustrate the parts and their relationships to one another.
First Pass Yield
First Pass Yield is a measure of quality in a process that reflects the percentage of product made correctly without any rework or corrective activity.
Generative Design
Generative Design uses Artificial Intelligence (AI) to generate the optimal design for system design requirements. This includes loads, constraints, preferred materials, and manufacturing processes.
Geometric Dimensioning & Tolerancing (GD&T)
Geometric Dimensioning and Tolerancing (GD&T) is a system for defining and communicating engineering tolerances and relationships. It uses a symbolic language on engineering drawings and 3D models that explicitly describe nominal geometry and its allowable variation. Additionally, it tells the manufacturing staff and machines what degree of accuracy and precision is needed on each controlled feature of the part.
Improve Global Product Development
Efficiently and securely achieve labor, wage, and market proximity advantages through global product development.
Intellectual Property (IP)
Intellectual Property is the characteristics of a design the owner may wish to protect from unauthorized use. Strategies include trade secrets, legal IP protection such as utility patents & design registration, and securely achieving labor, wage, and market proximity advantages through global product development.
Model Based Definition (MBD)
MBD defines the source of Product and Manufacturing Information (PMI) as the 3D model (Model-Based). The goal of MBD is to provide a “single source of truth” for downstream partners. For example, Manufacturing, Quality, Inspection, Service & Suppliers. MBD is a process that starts with an annotated 3D model. Using MBD, the 3D model replaces the 2D drawing as the source of PMI, but it can continue to support 2D processes.
Model Based Enterprise (MBE)
MBE goes beyond MBD, relying on a complete digital thread. Fundamentally, MBE utilizes the MBD to create downstream deliverables. Examples include NC toolpaths, manufacturing planning information, tool design, design collaboration, review & validation, inspection, and service information.
Model-Based Systems Engineering (MBSE)
Model-Based Systems Engineering (MBSE) is the practice of developing requirements, design, analysis, verification, and validation activities. It begins in the conceptual design phase and continues throughout development and later life cycle phases. These models provide an efficient way to explore, update, and communicate system aspects to stakeholders, while significantly reducing or eliminating dependence on traditional documents. MBSE is the application of modeling systems as a cost-effective way to explore and document system characteristics. By testing and validating system characteristics early, models facilitate timely learning of properties and behaviors, enabling fast feedback on requirements and design decisions.
New Product Introduction (NPI)
A New Product Introduction (NPI) program encompasses all the activities within an organization to define, develop, and launch a new or improved product.
Original Equipment Manufacturer (OEM)
An Original Equipment Manufacturer is a contract manufacturer that produces complete, finished products to the design and specification of a brand which another brand then distributes. It is a common business model, with many brands outsourcing some or all of their production (to OEMs).
Printed Circuit Board (PCB)
A Printed Circuit Board (PCB) mechanically supports and electrically connects electronic components using conductive tracks, pads, and other features. These components are etched from copper sheets and laminated onto a non-conductive substrate. PCBs can be single-sided (one copper layer), double-sided (two copper layers), or multi-layer.
Programmable Logic Controller (PLC)
A PLC is a computer used to collect data and automate control processes in factory and industrial equipment such as control motors, pumps, lights, fans, circuit breakers, and other machinery.
Product Manufacturing Information (PMI)
In traditional design documentation, an engineer adds pertinent data to a 2D drawing. This information likely includes annotations, surface finishes, geometric dimensions & tolerancing (GD&T), and notes. Collectively, this is called PMI. When engineering organizations transition to MBD, they add all the PMI to a 3D model instead of 2D drawings. PMI is a critical data component of a 3D model that enables Model-Based Engineering (MBE).
Quality Assurance
Quality assurance (QA) attempts to improve and stabilize production (and associated processes) to avoid or minimize issues that lead to a product’s defects.
Quality Control
Quality control (QC) is a process in which the quality of all factors involved in production is reviewed. It emphasizes testing products to uncover defects and reporting to those who allow or deny product release.
Rapid Prototyping (RP)
Rapid Prototyping is the use of various technologies to produce a prototype directly from 3D CAD data. This produces a result far more quickly than traditional model-making.
Semantic PMI
Semantic PMI is the annotations and attributes associated with a 3D solid model and its geometry features. They are software-interpretable and can be displayed for human interpretation.
Time to Market (TTM)
Time to market (TTM) is the length of time it takes from a product’s conception to its availability for sale. Time to market is very important as being late erodes the addressable market to whom you are selling your product.
Time to Production
Time to production is the amount of time it takes to produce a product. Reducing time-to-production brings products to market faster than current manufacturing ramp-up processes allow.
Manufacturing Terminology
Distributed Control System (DCS)
A Distributed Control System (DCS) is an automated control system that monitors and provides instructions to different machine parts. Commonly used in manufacturing equipment, a DCS utilizes input and output protocols to control distributed equipment. DCS systems are commonly used in process industries controlling breweries, refineries, chemical plants, and paper mills.
Downtime - Planned & Unplanned
Scheduled downtime is downtime due to planned events such as performing maintenance to equipment or installing upgrades or enhancements. Notifying staff of the planned downtime will allow them to make the preparations needed to ensure business operations continue in a safe and effective manner. For most manufacturers, downtime is the single largest source of lost production time. Unplanned downtime is downtime that occurs unexpectedly or because of a failure. Examples include hardware failure or waiting on appropriate materials to complete a task. Common categories of unplanned downtime include excessive tool changeover, excessive job changeover, lack of operator experience, and unplanned machine maintenance. When unplanned downtime occurs, no value is being produced but the cost of overhead operations continues to grow, which directly impacts a company’s bottom line.
Energy Costs
Manufacturing businesses are striving to reduce their energy costs associated with usage, as they continue to rise. The planet is negatively affected by industrial energy use which has increased government regulations requiring energy reduction & lowering carbon footprint.
Equipment/Machine Uptime
Machine Uptime measures the efficiency and availability of the company’s manufacturing machinery. It is defined as the total amount of time manufacturing equipment is in operation divided by the total amount of time in which the manufacturing equipment is scheduled for use over the same period of time, as a percentage.
Historian
Historian is a type of database designed to archive automation and process data regularly. This data is used to troubleshoot processes, optimize manufacturing, or increase regulatory compliance and traceability. Due to the enormous amount of process data some plants produce, some historians compress data using algorithms. Other historians are designed to act as a “rolling buffer” and can store high-frequency data.
Human Machine Interface (HMI)
Human Machine Interface (HMI) is a software application (typically a Graphical User Interface or GUI) that presents information to the operator about the state of a process and accepts and implements the operator’s control instructions. It may also interpret the plant information and guide the interaction of the operator with the system. Also known as Man Machine Interface (MMI).
Line Balancing & Takt Time
Line balancing is a production strategy that involves balancing operator and machine time to match the production rate to the takt time. Takt time is the rate at which parts or products must be produced to meet customer demand For a given production line, if production time is exactly equal to takt time, then the line is perfectly balanced. Otherwise, resources should be reallocated or rearranged to remove bottlenecks or excess capacity. In other words, the quantities of workers and machines assigned to each task in the line should be rebalanced to meet the optimal production rate.
Manufacturing Capacity
Manufacturing capacity is the maximum possible output of a manufacturing business, measured in units of output per period. Capacity is increased either to meet an actual (immediate) increase in customer demand or an anticipated (future) increase in customer demand.
Immediate capacity increases can be achieved by:
- Using Existing Equipment For More Time (Adding Shifts or Overtime)
- Using Someone Else’s Equipment (Outsourcing)
Future capacity increases are usually achieved by:
- Using Existing Equipment More Effectively (Improving)
- Purchasing New Equipment (Spending)
Manufacturing Cycle Time (also known as Throughput)
Manufacturing cycle time is the amount of time required for a product to pass through a manufacturing process, thereby being converted from raw materials into finished goods. The concept also applies to the processing of raw materials into a component or sub-assembly. The time required for something to pass through a manufacturing process covers the entire period from when it first enters manufacturing until it exits manufacturing.
Manufacturing Execution System (MES)
An MES is a system to manage, monitor, and synchronize the processes involved in manufacturing. MES coordinates the execution of work orders with scheduling, and ERPs/MROs, while capturing process performance, traceability, and genealogy.
Manufacturing Ramp-Up Time
Manufacturing ramp-up is a necessary phase of new product introduction in which planning and execution need careful consideration. The term ramp-up refers to when a company substantially increases its output in response to increased demand or an expected increase in the near term. Ramping up is costly and requires large capital investments in equipment and capacity. If demand does not last or is smaller than expected, a firm may be left with excess capacity.
Manufacturing Resource Planning (MRP)
Manufacturing Resource Planning (MRP) is a method for the effective planning of all resources of a manufacturing company. Ideally, it addresses operational planning in units and has a simulation capability to answer “what-if” questions.
Master Terminal Unit (MTU)
A Master Terminal Unit (MTU) is a device in a SCADA system that issues commands to the Remote Terminal Unit (RTU) which is located in remote places. MTUs are centrally located (typically at headquarters). The MTU gathers the required process data, stores the information, and aggregates the data from multiple RTUs.
Message Queuing Telemetry Transport (MQTT)
Message Queuing Telemetry Transport (MQTT) is a lightweight publish/subscribe protocol designed for SCADA and remote networks. It focuses on minimal overhead (2-byte header) and reliable communications. MQTT requires the data source to connect and publish data to a topic on an intermediary broker. Consumers can connect to the broker and subscribe to data from the topic.
Overall Equipment Effectiveness (OEE)
OEE is a metric identifying the percent of production time that is truly productive. OEE score of 100% represents perfect production. This would mean manufacturing only good parts, as fast as possible, with no downtime. Best-in-class manufacturers operate around an 85% OEE.
Overall Labour Effectiveness (OLE)
Overall Labour Effectiveness (OLE) is a KPI that measures the utilization, performance, and quality of the workforce and its impact on productivity.
Polling
Polling is the process in which a number of peripheral devices, remote stations, or nodes within a plant-based or SCADA network are accessed by a client application via a server to read and write data.
Production Run Setup Time
Production Run Setup Time measures the number of minutes required to set up an operational production run, from the completion of the last unit of a run until the completion of the first unit of the next run.
Programmable Automation Controller (PAC)
Programmable Automation Controller (PAC) is an industrial device similar to the PLC. Many hardware vendors use the term PAC to distinguish next-generation products from legacy controllers. A PAC is geared toward complex automation system architectures composed of a number of PC-based software applications, including HMI functions, asset management, historian, advanced process control, and others. Generally, a PAC tends to provide greater flexibility in programming, larger memory capacity, better interoperability, and more features and functions over a PLC.
Programmable Logic Controller (PLC)
A programmable Logic Controller (PLC) is an industrial device that provides an interface for input sensors and output actuators. PLCs can be programmed using relay ladder logic to control the outputs based on input conditions or algorithms contained in the memory of the PLC. Typically PLCs are used for simple and high-speed machine control. Common characteristics of PLCs are simple program execution scans, limited memory, and a focus on discrete I/O with on/off control.
Quality Management System (QMS)
A QMS is a formalized system that documents processes, procedures, and responsibilities for achieving quality policies and objectives.
SCADA
SCADA is a system of software and hardware elements to help control industrial processes. The system monitors, gathers, and processes data and supports direct interaction with devices such as sensors, valves, pumps, motors, and more through an HMI. HMI or Human Machine Interfaces reside on shop floor assets and are a component of the SCADA.
Scrap and Rework
Scrap and rework is defined as material that is added into production but is not part of a finished product. The cost of this scrap material does not add value to the organization, so it gets included in the calculation for the total cost of quality, or poor quality. This measure sums all costs associated with poor quality or product failure, including rework, scrap, warranty costs and other costs incurred in preventing or resolving quality problems.
Yield
Yield refers to the percentage of non-defective items of all produced items. It is indicated by the ratio of non-defective items to the number of manufactured items.
Service Terminology
Customer Self-Service
Customer self-service and support is a blend of customer-initiated interaction technologies designed to enable customers to service themselves. It includes electronic records management systems, chat, and knowledge bases.
Customer Uptime
High equipment uptime is the most important proof-point for customers evaluating service value. Equipment Uptime measures the efficiency and availability of the company’s machinery or equipment. It is defined as the total amount of time equipment is in operation divided by the total amount of time in which the equipment is scheduled for use, as a percentage.
Equipment Commissioning
Equipment commissioning is the process of ensuring all systems and components of the equipment are installed, tested, operated, and maintained according to the operational requirements of the owner. A commissioning process may be applied to both new projects and existing units. All systems are subject to expansion, renovation, or revamping.
First Time Fix Rate (FTFR)
First Time Fix Rate (FTFR) indicates the percentage of time a technician is able to fix an issue the first time.
Mean Time to Recovery (MTTR)
Mean time to recovery is the average time required to troubleshoot and repair failed equipment and return it to normal operating conditions. Mean time to recovery includes the time it takes to find out about the failure, diagnose the problem, and repair it.
Mean Time to Repair (MTTR)
Mean time to repair (MTTR) is the average time required to repair failed equipment & return it to normal operating conditions. This includes repair, testing, and time to return to normal operating conditions. MTTR is a basic measure of how maintainable an organization’s equipment is and, ultimately, reflects how efficiently an organization can fix a problem.
Mean Time to Repair vs. Mean Time to Recovery
*view bottom of section
Service Contract Renewal
A service contract renewal is a business agreement between a company or contractor and their customer. It covers the maintenance and servicing of equipment over a specified period and outlines the terms of a particular service between the two parties. The contract renewal rate indicates the percentage of contracts due to expire in a specific period that are successfully renewed. Contract Renewal Rate provides a good indication of the number of relationships a business can sustain and can help identify attrition and retention trends and underlying causes.
Service Dispatches
Service visits are often described as “truck rolls,” “service dispatches,” or “technician dispatches.” These are defined as a situation where a technician must be dispatched to a customer location for service, such as to repair a piece of equipment or perform a technical service. This type of dispatch happens when the customer cannot troubleshoot or repair the equipment themselves. The cost per dispatch can range from $150 to $1,000 a call depending on the service organization and industry. This affects costs, equipment availability, and in some cases, response time.
Service Level Agreement (SLA)
An SLA defines the level of service expected by a customer from a supplier, laying out the metrics by which that service is measured, and the remedies or penalties, if any, should the agreed-on service levels not be achieved. It pulls together information on all contracted services and their agreed-upon expectations into a single document. These documents clearly state metrics, responsibilities, and expectations. In the event of service issues, neither party can plead ignorance. SLAs ensure both sides have the same understanding of requirements. They should be aligned with the technology/business objectives of the engagement. Misalignment can negatively impact deal pricing, quality of service delivery, and customer experience.
Service Offering
A service offering is the service commitment that defines the level of service in terms of, for example, availability and price. With margins from product sales declining, service offerings are an increasingly important part of an OEMs overall business in terms of both revenue share & profitability.
Service Revenue
When margins from product sales decline, manufacturers look to services to fill the profit gap & grow their businesses. This is called service revenue. Service organizations must decrease service costs and increase service quality & customer satisfaction if they want to succeed.
Spare Parts Inventory
A spare part, service part, repair part, or replacement part is an interchangeable part that is kept in inventory. They are used for the repair or replacement of failed units. Spare parts inventory is the idea that spare parts are capable of being used, but are not yet affixed to production machinery which creates inventory.
*
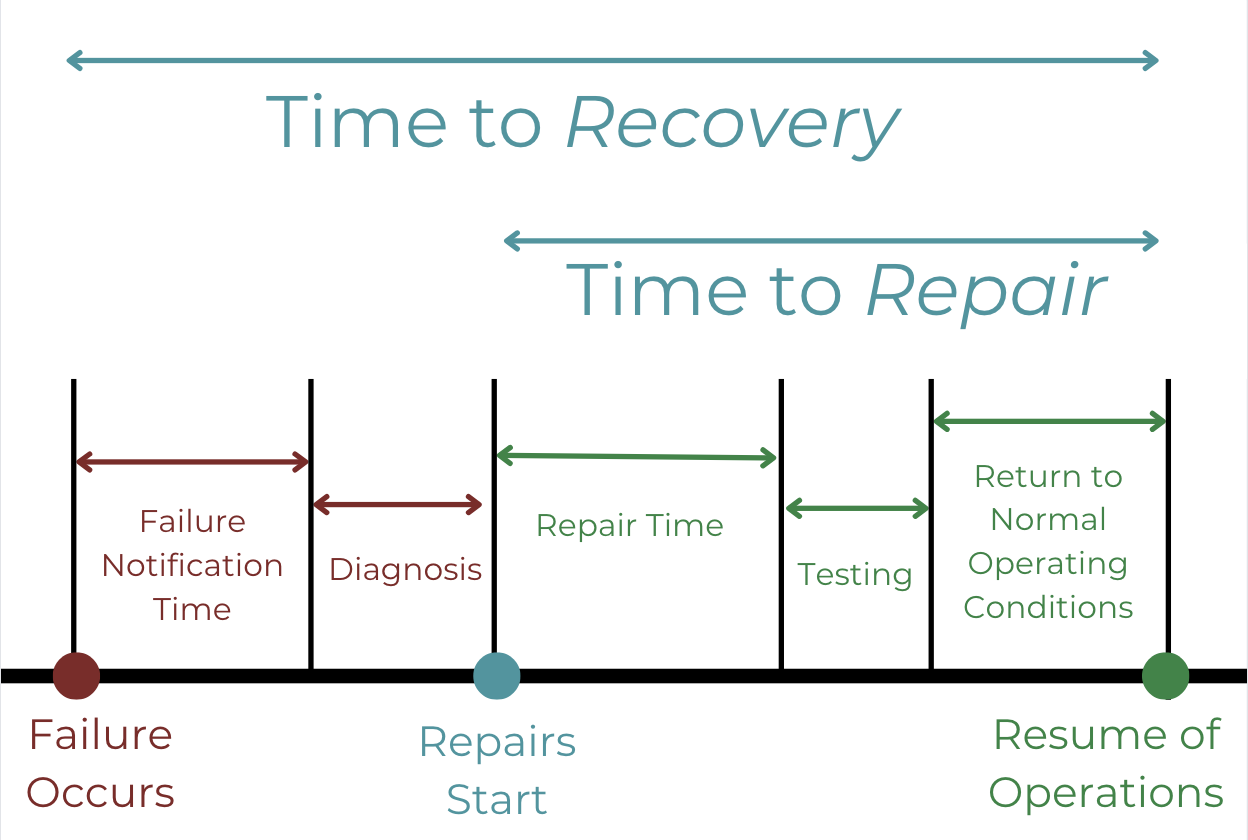
Sustainability Terminology
“Carbon-neutral” vs “Net-zero”
Carbon-neutral is a lesser claim than net-zero. A company may buy offsets to be carbon neutral such as planting trees to compensate for gas car trips. Net-zero, on the other hand, requires carbon to be avoided, like using EV cars charged with solar/wind sources. Net-zero also includes all greenhouse gases, not just CO2.
Carbon Disclosure Project (CDP)
The CDP is a global emissions reporting framework that many buyers accept from their suppliers. Well-scoring companies report emissions baselines, reduction targets, and reduction progress using trusted frameworks like SBTi. They also report climate risk analysis/mitigation using trusted frameworks like TCFD.
Circular Economy
A circular economy is an economic system aimed at eliminating waste and the continual use of resources. “Zero waste” is the objective.
Cradle-to-Cradle Assessment
Cradle-to-Cradle is a concept often referred to within the Circular Economy. It is a variation of Cradle-to-Grave, exchanging the waste stage with a recovery and recycling or remanufacturing process. This process makes all or part of a product reusable for another product, essentially “closing the loop” on the product’s life cycle. Businesses may also get their products Cradle to Cradle Certified.
Cradle-to-Gate Assessment
A Cradle-to-Gate assessment only evaluates a product’s life cycle up until the point it leaves the factory gates and before it is transported for distribution/use (i.e., raw materials extraction, processing of these materials, and manufacturing).
Cradle-to-Grave Assessment
A Cradle-to-Grave assessment evaluates all the phases in the life of the product from raw materials extraction, processing of these materials, manufacturing, dissemination/distribution, usage, maintenance, and repair, selling or reusing, and disposal.
Dematerialization
For manufacturers, dematerialization is the process of reducing the physical quantity of materials needed to produce goods, including tooling and waste byproducts. It focuses on reducing/replacing hazardous, expensive, and nonrecyclable material where practical. Replacing mechanical hardware with software is also a dematerialization method.
Environmental Product Declaration (EPD)
An Environmental Product Declaration (EPD) is a standardized document that describes a product’s environmental and human health impact. EPDs are governed by the ISO 14025 standard and derived from ISO-compliant Life Cycle Assessments (LCAs). They are also referred to as Type III EDPs. These third-party verified documents communicate the results of a product’s LCA, along with additional relevant environmental performance information at one of two levels, business-to-business (B-to-B) or business-to-consumer (B-to-C). Companies sometimes use these EPDs for commercial purposes, particularly in the building materials industry and for some consumer product categories in Europe.
Greenwashing
100% “sustainable products” or “circular products” don’t exist today in industrial markets. They’re inflated claims called “greenwashing”. Rather, “more sustainable products” or “more circular products” are honest labels for products that do better environmentally but are not yet perfectly zero-impact.
“Green” vs “Sustainability”
For our industry, this is best explained with examples. Windmills and solar panels are “green” products. They intend to completely avoid environmental damage via fossil fuel extraction and burning. Sustainability refers to doing things in a way that is less damaging to future generations and the future of the environment. For example, an electric motor is more sustainable than a gas engine. The motor’s intent is to move humans (not to save the planet) but does so in a way that will be less damaging than the engine to future generations.
Life Cycle Assessment (LCA)
A Life Cycle Assessment (LCA) is defined as the systematic analysis of the potential environmental impacts of products during their life cycle. During a Life Cycle Assessment/Analysis, you evaluate the potential environmental impacts throughout the entire lifecycle of a product. This includes production, distribution, use, and end-of-life phases. Additionally, it includes the upstream (e.g., suppliers) and downstream (e.g., waste management) processes associated with the production (e.g., production of raw, auxiliary, and operating materials), use phase, and disposal (e.g., waste incineration). The International Organization for Standardization provides guidelines and requirements for conducting a Life Cycle Assessment according to ISO 14040 and 14044.
Life Cycle Impact Assessment (LCIA)
A Life Cycle Impact Assessment is the evaluation of the potential environmental impacts by converting the LCI results into specific impact indicators. It uses established impact categories, category indicators, characterization models, equivalency factors, and weighing values (e.g., climate change, eutrophication, acidification, ozone depletion, water use, etc.)
Life Cycle Inventory (LCI) Analysis
Life Cycle Inventory (LCI) analysis is a technical process that quantifies all inputs and outputs from the processes within a given set of system boundaries for a product. The inputs are energy and raw materials and the outputs are emissions to air, water, and soil. This includes solid waste generation, products, and co-products. LCI analysis is essentially a mass-energy balance of the system. LCI data forms the basis of the data used to conduct a Life Cycle Assessment.
SBTi – Science-Based Targets Initiative
The science-based targets initiative is a greenhouse gas measurement and reduction framework to track a company’s emissions and reductions. The goal is to stay in line with the Paris Accord’s 1.5C goal. CDP encourages the use of SBTi for driving down carbon emissions. SBTi in turn subscribes to measurement standards in the Greenhouse Gas Protocol
Task Force on Climate-related Financial Disclosures (TCFD)
The TCFD is a risk assessment and mitigation framework for identifying how climate change can affect a company’s long-term business and how the company adapts to it. CDP encourages the use of TCFD for risk management.
Conclusion
We hope this glossary clears up any confusing or unfamiliar terms. If you have any additional questions about engineering, manufacturing, services, or sustainability, contact our experts.